
There are reasons to bring legacy equipment into the Industrial Internet of Things (IIot) Age.
Most manufacturers work with older equipment. A 2017 McKinsey report notes factory machinery and tools have an average age of 11 years. Industrial equipment lasts by design; we even use the term “industrial strength” to attribute higher-than-usual durability and power to everything from bug spray to boots. And when something is still working–and working well–a full upgrade to something new can be a difficult sell.
But many of these older legacy systems were created before the age of connected manufacturing systems, which bring with them a number of added benefits. A connected “smart factory” can mean higher productivity, increased flexibility, a safer manufacturing floor, and lower costs.
One option that bridges the gap between a full upgrade and missing out on all these benefits is to perform a retrofit of connected IoT gateway and data feedback devices. But until recently, this kind of upgrade was a complicated and costly affair. But it doesn’t have to be anymore, and more options are available.
What is the Industrial Internet of Things?
IIoT or the Industrial Internet of Things is the industrial extension of IoT. Automation in a traditional factory improves through the use of interconnected smart sensors. Other instruments work with sensors to take advantage of data collection and analysis. This happens on a networked (Internet) platform.
Options for Connecting your Factory Floor
There are several options now available for connecting your legacy systems to the IoT. These include
- Retrofitting IIoT Connectivity. IoT gateways use software, sensors, and industrial-based control systems to provide a simple connection that can send data in real-time.
- Using Video Cameras. Video analytics allow cameras to recognize objects, people, or issues on your floor automatically.
- Using Edge Devices. Data can be accessed via local devices. This can improve security and provide access to process data more quickly.
- Using Biometric Devices. Your employees can become part of your data acquisition through the use of biometric wearables or tags. This works in conjunction with additional upgrades.
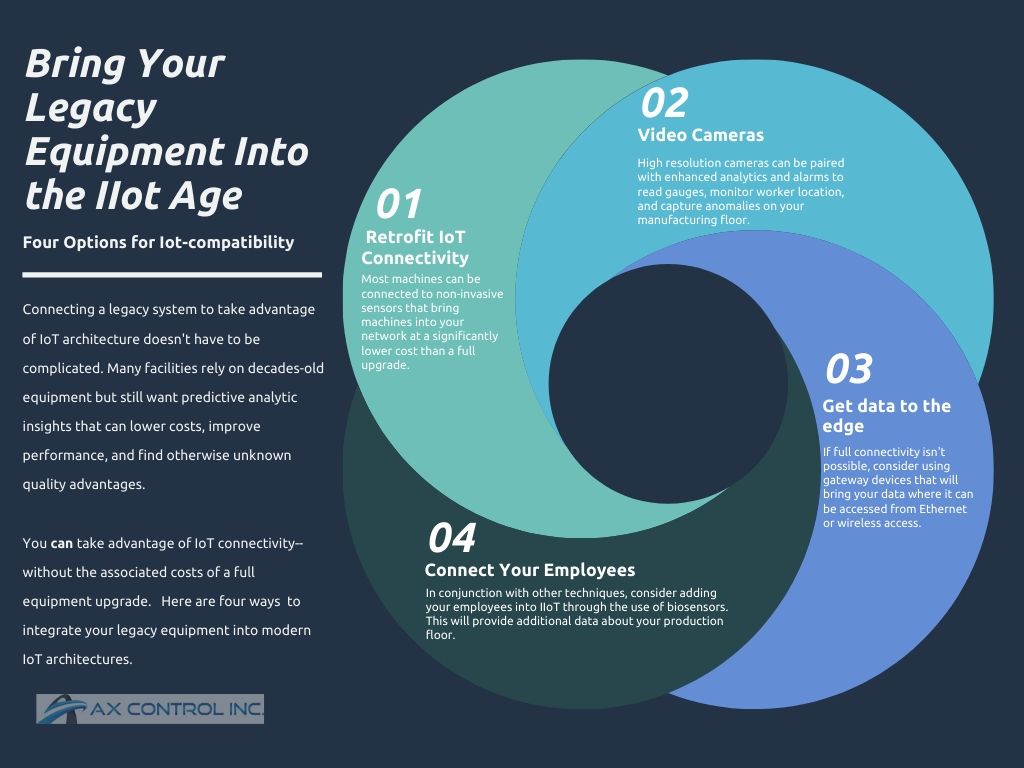
You must be logged in to post a comment.