Speedtronic turbine control from General Electric is one of the world’s most reliable turbine control systems. Find out more below.
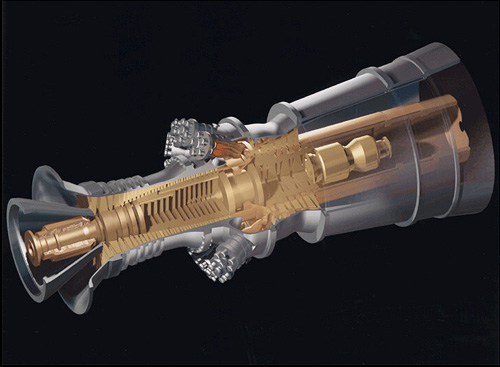
A History of Turbine Science
Gas turbine theory is not new to the world; in fact, Leonardo Da Vinci designed a reaction-type turbine. While nothing like the turbines of today, Da Vinci’s chimney jack’ used hot air rising from a hearth to turn an axial rotor attached to a roasting spit located over the fire. In this way, food on the spit turned without need for an attendant, harnessing the power of burning gases.
Early History
GE was one of the first modern companies to understand the power of turbine applications. High-profile projects like Niagara Falls (1918) and the Grand Coulee Dam project (1942) used GE turbines. The first gas turbine used to generate electric power in the US came from General Electric. It was a 3.5-MW unit installed at Belle Isle Station, Oklahoma City, OK, in 1949.
Expansion of Products
GE’s gas turbine division is now over a century old. It has advanced gas turbine jet engine design along with commercializing industrial gas turbines for the first time. GE turbines are also used for power generation. You can find them in nuclear power plants, combined-cycle gas turbine plants, and in steam turbine systems and boiler systems.
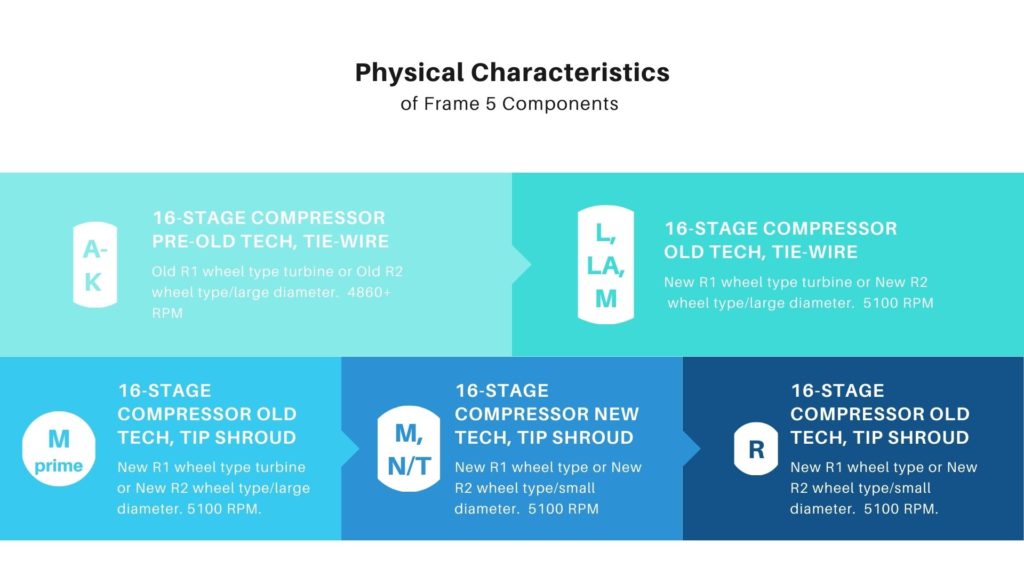
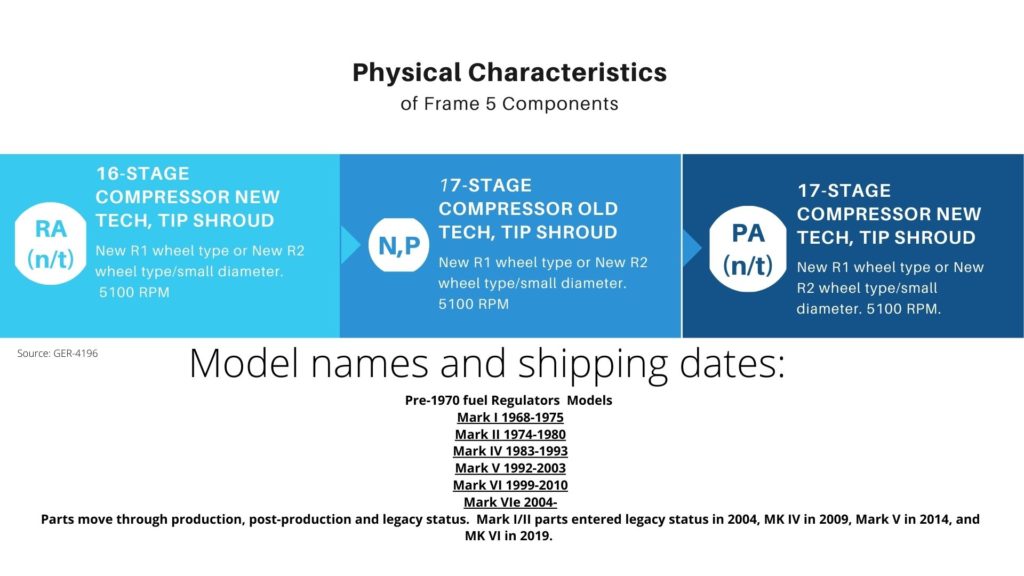
Introduction of Speedtronic Turbine Control
Beginning in the 1960s and continuing through the early 2000s, GE developed and sold sophisticated turbine control systems for their gas and steam turbines. These systems sold under the SPEEDTRONIC trademark name. Speedtronic systems started with the Mark I series, continuing through the release of the Mark VIe.
While each system had significant improvements, many Mark I and Mark II control systems are still in active use around the world today. The longevity of these systems is attibutable to GE’s adherence to specific gas and steam turbine control philosophies. These emphasize “safety of operation, reliability, flexibility, maintainability, and ease of use, in that order,” according to company documents. The gas philosophy maintains:
Continue reading “A History of GE Speedtronic Turbine Control”
You must be logged in to post a comment.