Electrical equipment has the same need for air and cooling as human beings. Without a proper air supply, machines will flounder and fail. You have to protect equipment from heat damage, or they’ll die. But these expensive casualties don’t have to occur.
Pull out the manual for any equipment in your plant, and you’ll probably see a bolded notation stating its proper operating temperature range. Keeping equipment operating within this range makes sure those machines remain an efficient and reliable part of your operation, and avoids the cost associated with failures like unexpected shutdown, deteriorated performance, and shortened equipment life, not to mention the need to replace damaged equipment.
Sustaining proper operating temperature is especially important in CNC machines where machine precision can be affected by thermal errors. Machines running outside their proper operating range have significantly more errors than those running within range.
Is basic maintenance enough?
Basic maintenance is a good first step for protecting equipment. The primary source for damaging heat comes from within the equipment’s own enclosure. As temperatures increase, lifespan decreases: a 10C change can cut a machine’s lifespan in half. While new, clean equipment can easily maintain proper operating temperature, internal temperatures will increase as particulate matter like dust, debris, pollutants, or dispersed oil sit on the surface like a thermal blanket and create a topical barrier.
Additionally, these contaminants increase the humidity within the enclosure through attracted water vapor, which can cause corrosion and other ill effects.
- Predictable: makes budgeting and planning of resources possible
- Assuring: you are aware and ahead of problems
- Wise: preventive maintenance is logical, easily understood, and justifiable.
- Non-reactive: prevents the majority of problems, and reduces forced outages. Typically reduces overall maintenance costs.
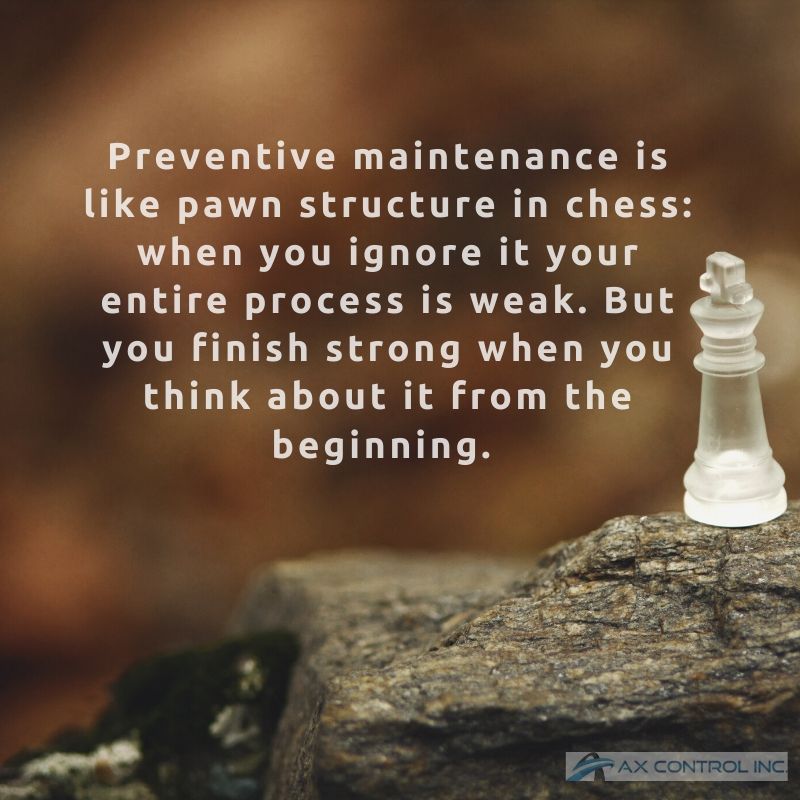
Maintenance schedules as noted within manufacturer guidelines should be followed to reduce or eliminate heat build-up and excess humidity. However, these schedules may be designed for “average” use. This may not apply to your situation if the equipment is a cornerstone of your plant’s output. To further reduce operating temperature, it may be advantageous to place equipment away from direct sunlight, away from other heat sources, and–if possible–near an air source like a filtered fan or near a heat exchanger.
It may also be helpful to determine heat sources beyond those within the spindle motor and machine base, such as the heat created during cutting, or heat built up over longer than average run times, using spot sensors to examine actual temperature readings around the machine. This type of data can help with the development of an optimized cooling plan that will increase the efficiency and accuracy of equipment while decreasing overall operating costs.
Why maintenance is important
When the demand for your product is high and time is short, it’s easy to sideline the servicing of equipment. But regularly scheduled maintenance now will extend your equipment’s lifetime, improve its efficiency, and prevent unexpected interruptions that will significantly affect your production schedule when you can least afford it.
Proper maintenance also helps prevent accidents. Many things can go wrong with faulty equipment, and the longer a problem goes undetected, the bigger the safety issue it presents to your workers. The cost of equipment repair will always be less expensive than equipment repair plus the cost of covering medical bills for workers injured because of equipment issues.
Finally, you’ll want those detailed repair records when it’s time to upgrade. They’ll increase the value of your old equipment. Potential buyers want to have confidence equipment has been well-maintained over its lifespan before they choose to purchase it, and are often willing to pay more for the peace of mind that comes with documented upkeep. This higher resale value will help offset the cost of the new equipment moving on to your production floor.
Are you ready to upgrade your plant equipment? Call AX Control about selling us your surplus.
You must be logged in to post a comment.