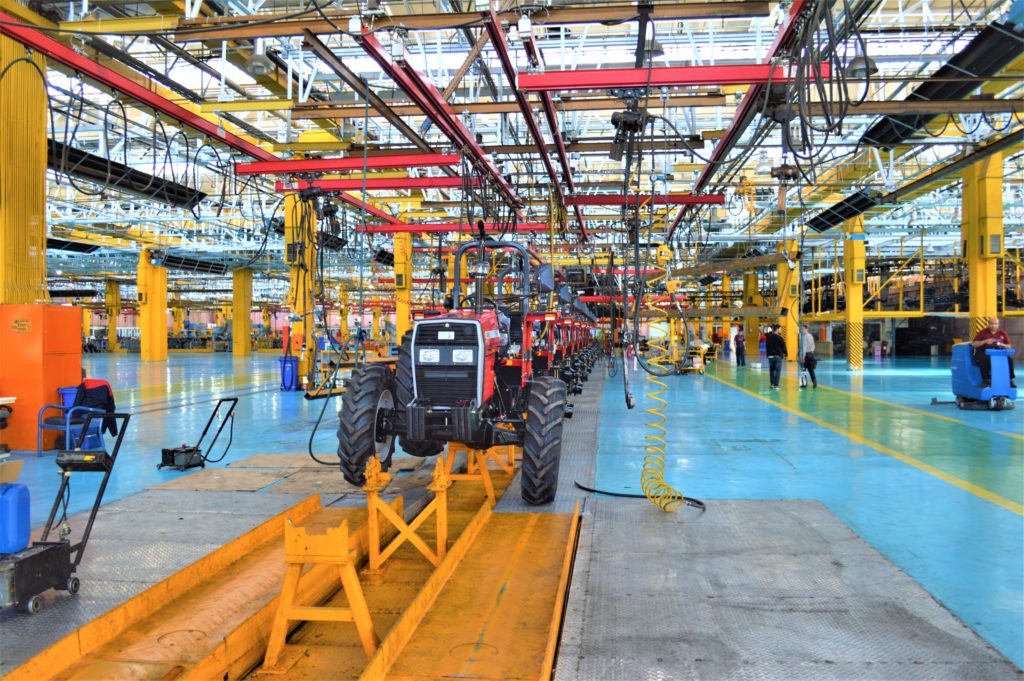
Anyone who works in manufacturing knows unexpected machine repairs can lead to production loss and downtime. They can even result in injuries. Better to prevent issues altogether. Read on to find out how.
Downtime is Deadly. Machine Repairs are Key.
In this competitive global economy, a reliable and efficient operation is key to reducing costs and staying on top. But if regular maintenance is ignored for too long, industrial machines will choose their own time to break down, often with catastrophic consequences.
It doesn’t have to be that way. Regular machine repairs keep industrial-grade machinery humming and keep production on schedule. Downtime decreases, safety issues decrease, and overall product quality goes up.
Here are some common machine failure points and the repairs that will keep your facility in tip-top shape.
Motors
Motors (like GE’s VersaMotion series) are the heart of many machines. The devices take incoming electrical energy and turn it into linear or rotational motion. While these components last a long time by design, certain conditions reduce their lifespan. These include
- Poor ventilation. Improperly ventilating a motor can allow dirt and other debris to enter the system. This can lead to overheated or shorted circuits, or fouled moving parts.
- Improper installation. Wear can occur if the motor is installed in the wrong place or without vibration mounts. A dust-proof housing helps maintain a clean interior.
- Poor lubrication. Without enough oil or the correct oil, motor components rub against one another. This increased friction can lead to permanent damage or failure of the unit.
- Overheating. Overloading the motor can result in overheating. But overheating can also happen if any of the previous three situations mentioned are present. Meanwhile, increased temperature increases the likelihood of motor failure.
Regular maintenance, including lubrication, cleaning, and replacing worn or damaged parts, can extend the lifespan of your motor. Make sure to check motors for problems during normal operation.
Machine Repairs and Bearings
Bearings exist in almost every industrial machine imaginable. The small parts reduce friction and smooth out rotation. They also help parts maintain proper position as they rotate.
Industrial-grade bearings have low-speed limits and high load ratings. Further, industrial bearings offer higher quality and better performance than traditional parts. They maintain top performance for manufacturing processes within industries like mining, oil and gas refining, and power production.
But the same qualities that make them suited for these industries also increase their cost. If you can extend their effective lifetime, it’s worth doing.
Common problems with bearings will present in several ways, including as:
- Surface damage on machinery shafts
- Bearing jams
- Noises within the machine during operation.
Most bearing problems can be identified and avoided through inspections and maintenance. Good and regular lubrication will maintain most bearings. However, without the proper lubrication, bearings will lose efficiency and will fail.
Gears and Belts
Components that transmit power from one location to another can also lead to machine repairs. Gears and belts drive all kinds of industrial machinery, and when they break, the device is often stopped dead until the part is fixed or replaced.
But gears and belts fail for a number of common and easily diagnosed reasons. These include:
- Material fatigue. This often happens after many user hours. Avoid stoppages through regular inspections.
- Vibration. Vibration can cause gear teeth to grind against each other and lock up.
- Overheating. Excess heat can cause gear expansion. This changes the grip between belt and gear, causing slippage.
- Mechanical shock. A sudden jerk can move machine components out of position, changing fit. Inspect regularly to avoid failure.
Regular Maintenance is Vital
Regular maintenance goes a long way to reducing unexpected machine repairs. Consider following OEM maintenance schedules to stay up-to-date with inspections and lubrication.
Also, remember that it’s important to delegate all machine repairs to qualified individuals. If your team doesn’t have the skill set to repair a particular piece of equipment, remember that AX Control offers machine repairs on components like drives, PLCs, PCBs, and HMIs. Talk to our team today if you need help!
AX Control is located in central North Carolina. Need a part fast? Ask to pick up at our facility.
Thanks for reading! Please feel free to share.
You must be logged in to post a comment.