
History of Lean Manufacturing
“Lean Manufacturing” as a term has only been around for a little over 30 years. The term was originally coined by John Krafcik (now CEO of Waymo and former CEO of Hyundai Motor America) in his MIT master’s thesis entitled “Triumph of the Lean Production System.”
Definition: Lean Manufacturing
a practice or process
that seeks to minimize waste while maximizing value to the customer or client.
While Krafcik may have created the term, lean manufacturing has been around for significantly longer. It can be traced back to the work of Eli Whitney, who was the first to successfully manufacture a product with interchangeable parts, and to time and motion studies by engineers like Frederick Taylor and Frank and Lillian Gilbreth applied to industrial workers of the early 20th century. Additionally, Henry Ford’s assembly line was also a leap forward in lean manufacturing.
The Toyoto Motor Company & Lean
Many feel the true cradle of lean manufacturing, however, was the Toyota Motor Company. When Toyota began producing cars in the years after World War II, it had to contend with low demand and limited financial resources. In order to strengthen its financial position, the company
“Out of clutter, find simplicity. From discord, find harmony. In the middle of difficulty lies opportunity.”
Albert Einstein
moved production to ‘build-to-order’ targeting, implementing the notion of “pull” instead of “push” or “just-in-time” manufacturing. They kept inventory as close to zero as possible and instead tried to produce cars as they were needed. This close-to-zero inventory is part of the modern lean philosophy.
By the time Krafcik wrote his thesis for MIT in the 1980s, the Japanese production management principles leading to the basic elements of lean production may not have been widely accepted, but they were well-enough known worldwide to creep into popular culture references like director Ron Howard’d 1986 movie Gung Ho. A few years after Krafcik’s paper, James P. Womack and others at MIT published “The Machine That Changed the World: The Story of Lean Production.” Suddenly–it seemed–everyone knew about lean.
Are There Limits to Lean in Manufacturing?
Lean practices can apply to any type of manufacturing process. This includes
- Repetitive Manufacturing that has a committed production rate. Repetitive manufacturing often uses dedicated production lines that never change output and have minimal setup requirements.
- Discrete Manufacturing that may also use production or assembly lines, but requires a number of setups and changeovers to meet changes in design output.
- Job Shop Manufacturing that uses production areas and produces smaller batches of made-to-order or made-to-stock custom products.
- Continuous Process Manufacturing focused on the production of raw materials like powders, liquids, slurries, or gases.
- Batch Process Manufacturing that, like above, processes raw materials. In this case, they run in discrete amounts to meet customer or consumer demand.
- Additive Manufacturing using 3D technology to create the end product.
How does Lean compare to Green Manufacturing?
Increasingly, sustainability and green practices are of concern to manufacturers. Not only are regulators and government agencies concerned about practices impacting the environment, so too are customers and stakeholders, meaning those companies ignoring green practices may lose business because of that lack.
While not perfectly overlapping, Lean’s emphasis on waste reduction and limited production does tend to make it an environmentally friendly process. Manufacturers who want to focus on green production should be able to tailor their lean process accordingly.
Lean manufacturing suggests limiting your spare parts inventory in order to limit cost output and to maintain Lean’s goals of waste reduction and order. However, you still need to stock the right parts to keep wasted time at a minimum. This means grouping parts into separate categories. Critical parts–the ones that stop your production cold when unavailable–should remain in stock at all times to limit downtime. Parts needed to keep equipment in good working order, while not as crucial, should also remain in stock, but at lower levels.
Limit or eliminate in-house costs through a strong relationship with a reliable vendor. Vendor relationships can be of particular importance when you’re running legacy equipment, where a well-stocked industrial automation supplier can essentially act as your off-site on-demand parts warehouse.
How are the Objectives of Lean Manufacturing Achieved?
The primary goals of lean manufacturing are to improve quality and eliminate waste while reducing costs and time.
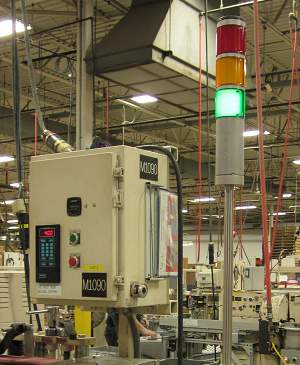
- Improve quality. Understand and respond to the customer’s needs and wants. Design processes to improve information and production flow to meet customer expectations.
- Eliminate waste. This includes direct waste like unproductive work hours for employees or machinery, as well as waste from overproduction and defects. Waste can also come from too much motion, either in the transportation of products or from workstations being too far apart.
- Reduce costs. Produce only to customer demand (JIT.) Reduce errors. Avoid delays that will create re-work, misdeliveries, etc.
- Reduce time. Efficient time management is one of the best ways to lower costs and eliminate waste.
Definition: What is 5S?
5S was developed in Japan. It enabled the Toyota Production System known as “Just In Time” or JIT manufacturing that became known as Lean manufacturing in the 1990s. 5S has five phases:
1. Sort: Eliminate unneccesary items. Store them away.
2. Straighten: Give necessary items a fixed location. Arrange all tools to be easily accessed and stored.
3. Shine: Clean and inspect tools and workplace daily/often.
4. Standardize: Establish and keep a routine for 1-3.
5. Self-discipline: Maintain routine autonomously, as part of your culture.
6S adds 6. Safety: Identify hazards and keep workers safe during all work operations.
Additional Lean Principles
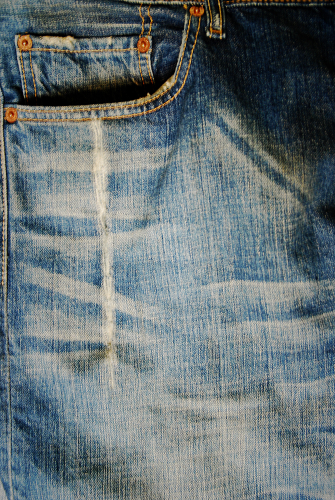
If you’re just beginning your journey of learning about lean manufacturing, you may feel a bit overwhelmed. There’s a lot to learn. It helps to realize lean manufacturing is not a static ‘one size fits all’ system. Instead, you should think of Lean more like your favorite pair of Levi 501s: off the rack, they could be anyone’s, but with time and care it’s like they were made for you. Lean manufacturing is similar in that you must put in the work, but eventually, the process becomes perfectly tailored for your organization.
Here are some of the tools/terms you may want to learn more about.
Agile Manufacturing
Considered to be ‘the next step’ beyond Lean, Agile Manufacturing is based upon the modular product design, investment in employee training, alliances with like-minded corporate partners, and rapid IT response.
Andon
An on-the-floor system allowing operators to stop the production process when needed (for quality) including a visual feedback system for assistance alerting, such as stack lights.
Heijunka
Lean method moving away from batch manufacturing toward a method allowing level manufacturing based upon volume or product type to create a stable workflow that will meet average demand.
Hoshin Kanri
Also known as policy deployment, Hosin Kanri ensures achievable company goals by removing poor communication and inconsistent direction along with its associated waste.
Kaizen
Action plan or philosophy, Kaizen is the continuous improvement by employees at all levels to create incremental improvements in the process.
Jidoka
“Automation with the human touch,” also known as Autonomation, Jidoka enables either machines or operators to detect and to stop work if a quality issue is detected.
PDCA, or Plan, Do, Check, Adjust
This 4-step process applies the scientific method to manufacture for continual improvement. Each step is done in order and constantly repeated:
- planning phase established objectives
- do phase tries tests, and gathers data
- check phase evaluates results
- adjust phase makes improvements as needed before the process repeats.
Takt time
This is the rate at which a finished product must be completed to meet customer demand. Takt is short for “takzeit,” a German word meaning ‘rhythm of music.’ The formula for Takt time is T/D, where T=available production time and D=daily demand. If you have a daily demand of 20 units and work an 8 hour day (480 minutes) your TAKT time would be 480/20, or 24 minutes per unit.
How To Implement Lean
Any organization looking to implement Lean processes should begin by learning more about Lean tools and theory. Once these are understood, leaders and organizational members can use the 4-step PDCA process to adopt Lean ways of thinking and begin to tailor your own Lean plan. Just remember, like that pair of jeans, a perfect fit does not happen overnight.
AX Control carries a variety of products from Reliance, GE, Fuji, Horner, and other manufacturers.
You must be logged in to post a comment.