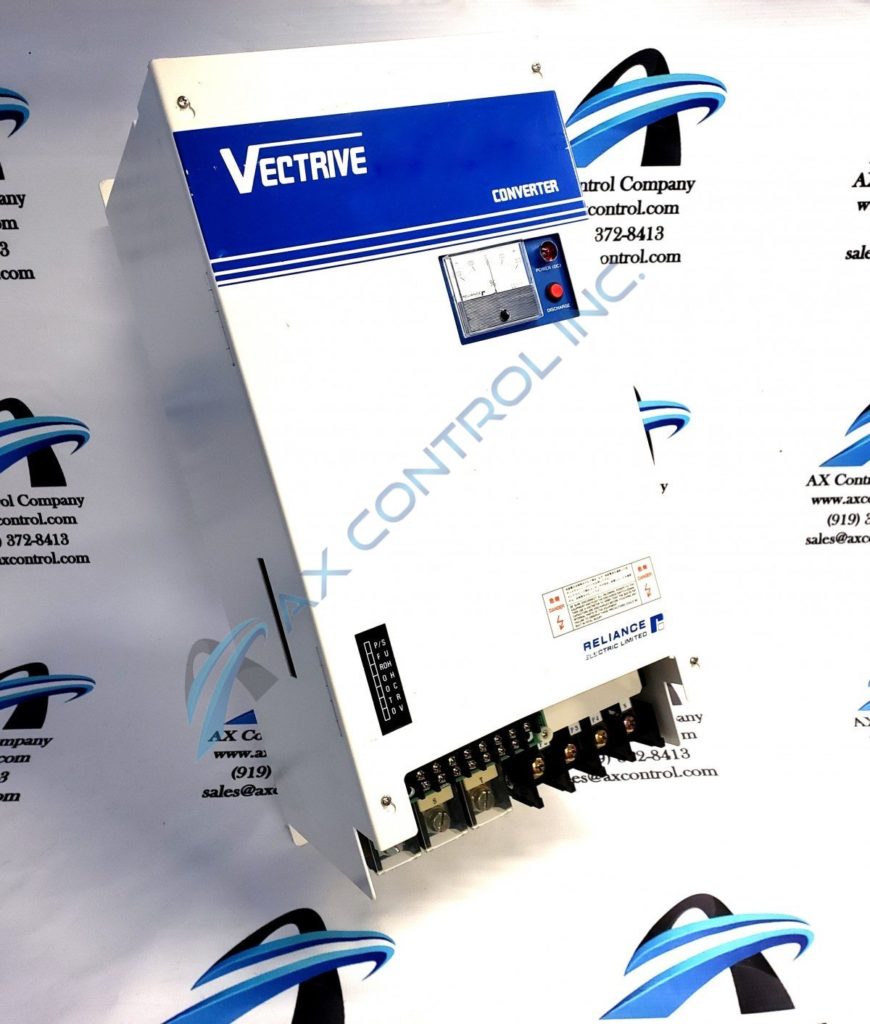
The servo drive of today is not the same as the basic power amplifier of yesterday. These complex equipment devices have dozens of available features that expand and improve their original motion control abilities. We don’t want you to miss out on any of these great features from lack of knowledge, so we’ve created a short blog post to introduce you to the top three features you should know about.
Auxiliary Feedback/Dual Loop Control
One important servo drive feature to understand is the auxiliary feedback/dual loop control option.
Servo drives read motor feedback, but many are also capable of reading an additional feedback source. This is called an auxiliary feedback. Typically, an auxiliary feedback is attached to the moving load, for example, connections in the drivetrain like gearboxes, couplings, or ball screws.
A system with two feedback devices has dual-loop control. Feedback on the load lets the system make adjustments as needed to compensate for problems like backlash or windup. Small adjustments create a more precise system overall.
The most common type of dual-loop control uses a rotary encoder to close the inner loop and create velocity control. Then a linear encoder is used for the position loop to determine proportional and integral gains. Use of dual rotary encoders is also possible.
STO, or Safe Torque Off
Safe Torque Off, or STO is a potentially life-saving feature built into many digital servo drives.
STO shuts motor power down instantaneously without powering down the servo. It acts much in the same way as a drive inhibit function.
But unlike an inhibit function, safe torque off creates a physical disconnect between power devices and motor phase terminals. This impedes the motor on a hardware level, making accidental start-ups nearly impossible.
STO creates a safer maintenance environment. Until several physical steps take place to manually disable STO, the motor cannot start up again. Meanwhile, the drive inhibit function can become accidentally bypassed. Imagine what would happen if an inhibit pin slipped during maintenance. The unexpected torque applied to machinery could injure or possibly kill workers.
It is important to note that, on some drives, STO mode does not block all movement. In fact, equipment can still move by hand or by gravity. Be sure to read manuals and user guides associated with your particular device for details on how your product handles STO mode.
Programmable Inputs and Outputs
Programmable inputs and outputs (programmable I/O) lets digital servo drives connect with each other and with other system elements through simple high/low voltage signals. The user designates these.
These inputs and outputs can act independently of the main controller or network I/O. This gives the entire system more flexibility, offering the chance to configure events like inhibit, jog, or enable a sequence from a specific servo. Outputs can trigger when only certain conditions like overspeed or position are met.
This capability offers the chance to create simple but useful routines within the system, like the triggering of a tone when a cycle completes or the activation of a warning light when motor rotation is present. But it is capable of more. Interconnected I/O can improve the safety, reliability, and synchronization of the overall system, especially in complex systems. Creating cascading action/reaction I/O interconnections maintains proper timing between individual servos and motors. Additionally, this sort of setup removes computational load from the controller and/or network.
AX Control maintains on-hand stock of many servo motors and drives. We specialize in GE products. Need a GE servo drive or motor? We can help!
Want to know more about servo position controllers? We have more information on our blog!
You must be logged in to post a comment.