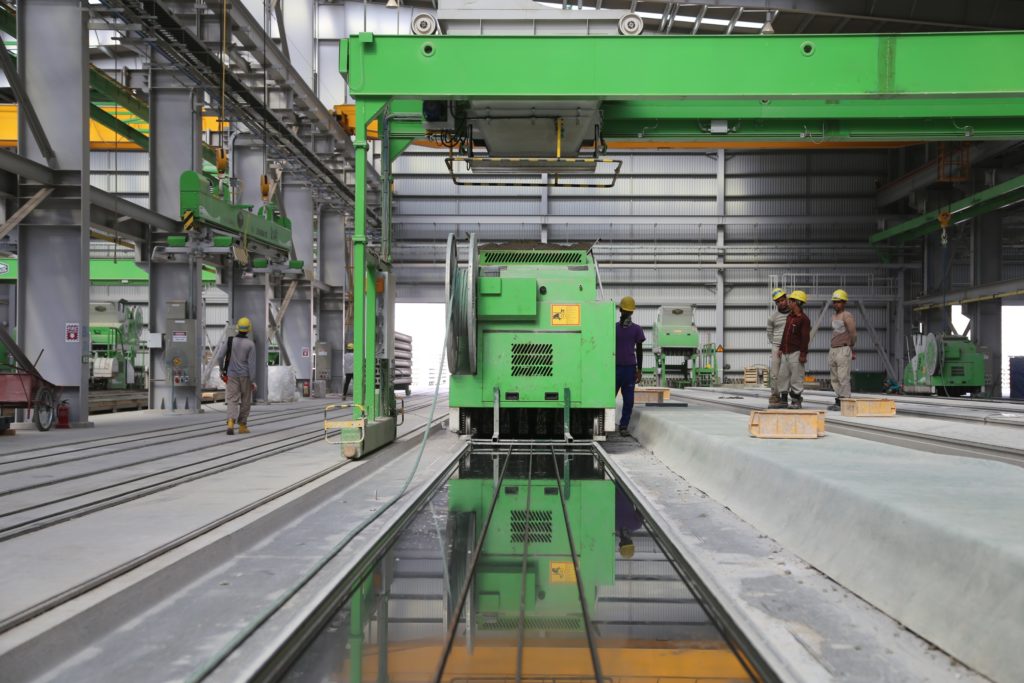
AX Control states at the top of our “About” page that we are “a global supplier of industrial automation parts.” But what exactly is industrial automation?
As a basic definition, “industrial automation” is the control of machinery and associated processes in industrial settings using computers, interfaces, software, and robotics. But let’s delve a little deeper.
Benefits of Industrial Automation
Some believe Henry Ford’s assembly line was the first example of industrial automation. But today industrial automation goes far beyond the assembly line. It includes the use of control systems run by robots or high-powered computers. Control systems run information technologies that take care of processes and jobs that were formerly the responsibility of human beings. The advantages of the change to automation are several:
- More consistent quality. An automated industry tends to produce uniform goods.
- Fewer accidents. A properly designed industrial automation system will take over any dangerous tasks in the manufacturing process, reducing the possibility of employee injury.
- Improved productivity. Automation significantly improves output, even when the associated labor force shrinks.
Related Automation Tools
Industrial automation impacts the manufacturing process in several ways, depending on the tool used. Here’s a list of the most common items used in industrial control.
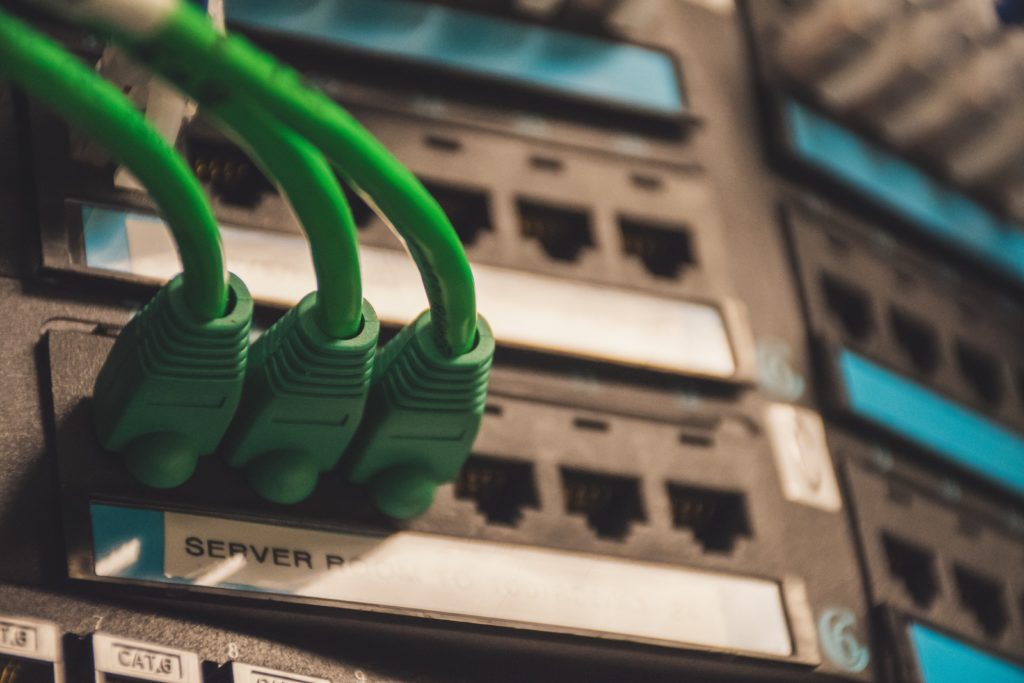
- DCS, or Distributed Control System. A DCS is a control system that relies on multiple control loops. The system has multiple autonomous controllers placed throughout it. These systems are used in large manufacturing processes like chemical or water treatment plants, oil refineries, or nuclear power plants. GE’s Speedtronic Mark IV was a DCS system.
- Robotics/Robots. Robots are machines that use machine learning to improve their processes. They can carry out complex actions automatically via embedded control or through programming from an external device. Robotics improve automation quality, increase production flow, and decrease the chance of employee injury by performing dangerous tasks.
- HMI, or Human Machine Interface. An HMI is a user interface that allows the operator (worker) to interact with the controller. This often includes a touch panel or a touchpad. But with IoT technology, HMIs can embed into mobile devices like smartphones.
- SCADA, or Supervisory Control and Data Acquisition. SCADA control systems use computers, GUIs (graphical user interfaces), and networked data communications for high-level commands. Real-time control calculations from field sensors and actuators are controlled by networked modules. This data is fed upward through several levels of control to the supervisory level. This translates and performs data analysis. SCADA is similar to DCS systems in function but uses various means to control all parts of the plant. Today’s industrial systems are more complex and often need connectivity through IoT data communications.
- PLC, or Programmable Logic Controller. A PLC is like a rugged industrial digital computer designed to control manufacturing processes. PLCs can hold up to harsh conditions even when used for a long time. Robotic devices and assembly lines use PLCs as part of their control systems.
Want more information about this subject? See our comprehensive list of industrial automation terms.
You must be logged in to post a comment.