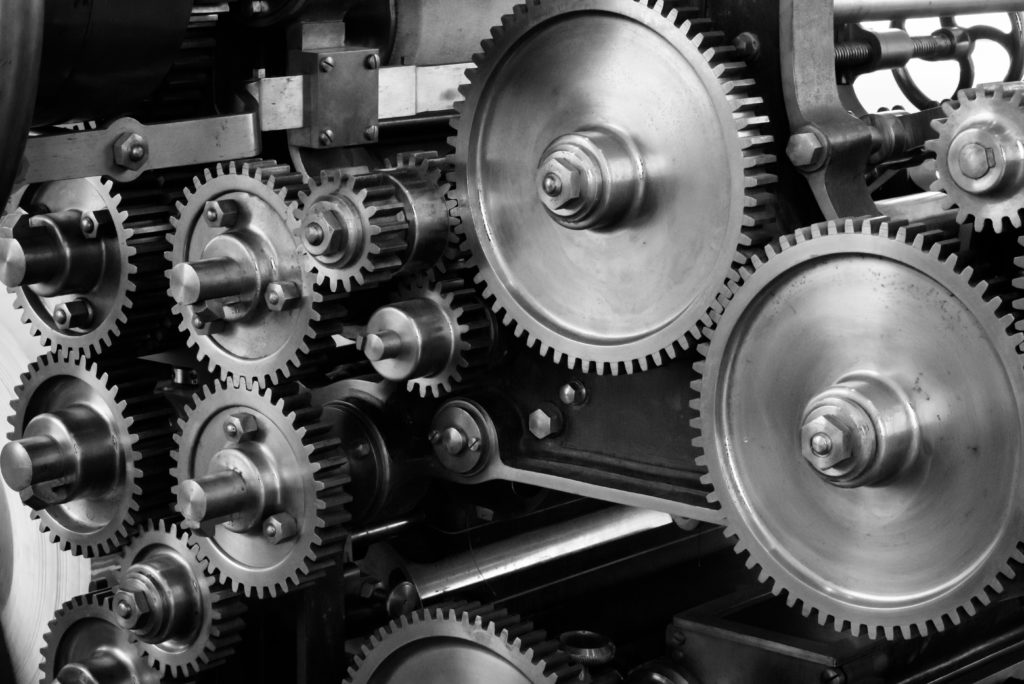
A closed-loop system will make automatic adjustments without external adjustment. The system uses a setpoint as part of the initial setup.
Sound difficult? It’s not. Let’s break that down.
Interacting With Closed-loop Systems
You’ve been using closed-loop systems for most of your life. You just didn’t know it.
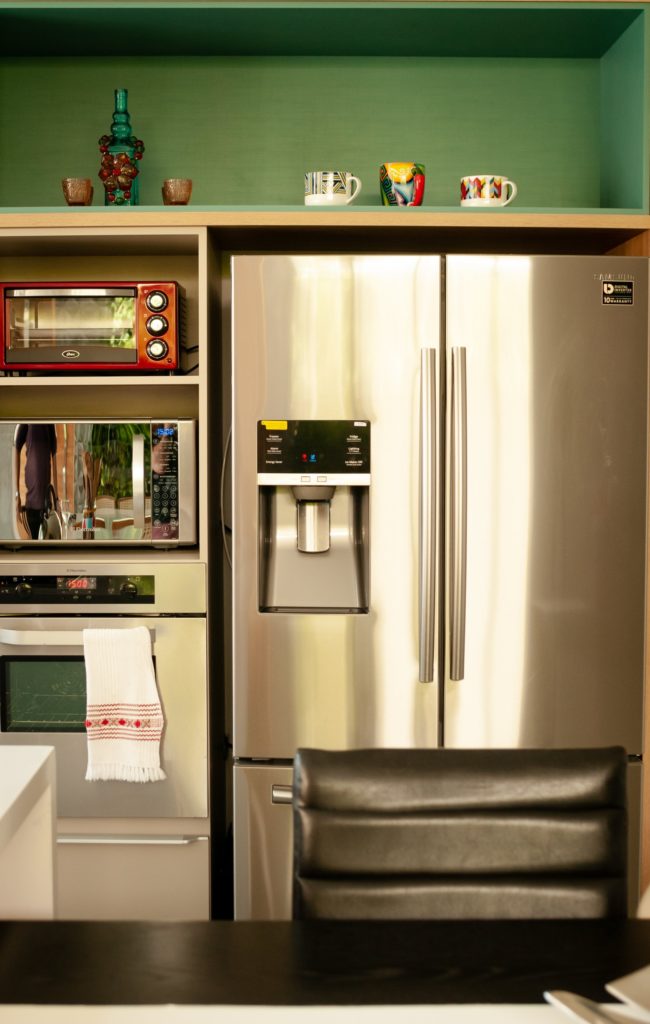
One of the most-used closed-loop systems in your kitchen is your refrigerator.
Think about the last time you went to grab a snack out of your fridge. Did you think about the temperature dropping as you stood with the door open, scanning the shelves? Probably not.
You didn’t have to, because your refrigerator motor and compressor will click on automatically to compensate for the change in internal temp. That’s what refrigerators do.
That’s a closed-loop system. The open door increases the interior temperature. A sensor automatically alerts the compressor to begin the cooling process again. This moves more refrigerant through your unit, creating evaporation, which cools the inside until the setpoint temperature is reached.
Other Closed-loop systems
Electric irons, air conditioners, and ovens are other examples of everyday closed-loop systems. Cruise control could also qualify as a closed-loop.
Take a look at our blog on bang-bang control if you want to know a little more about these kinds of control systems. That blog also explains a little about PID control, which works in a different manner.
Control Loops in Industrial Applications
Control loops also make up a fundamental building block in industrial control systems.
In the example below, the controller could be many things, including a PLC (programmable logic controller), DCS (distributed control system), a discrete controller like a GP3000 series industrial PC, or even a function block.
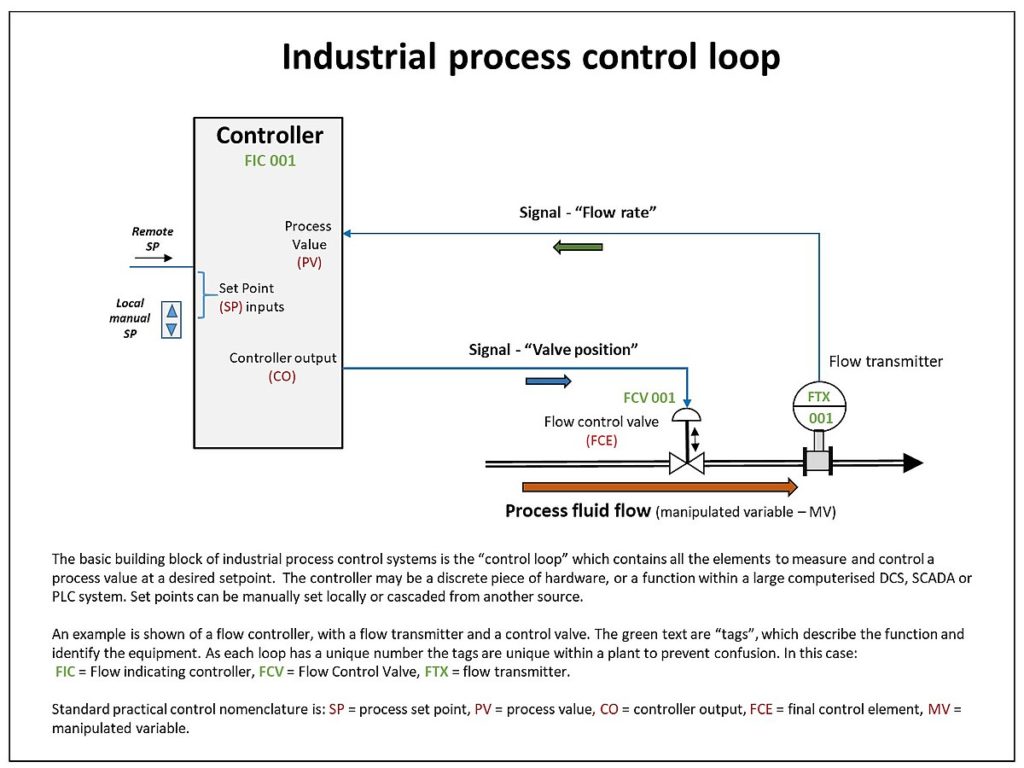
The above diagram is an example of a PID or intermediate control function that can generate any range of outputs. This means it can run at 1%, 50%, or 100%, or anything in between.
As the left-hand side of the diagram shows, these systems can accept set points (SP) either locally or remotely. Local input might be from a panel, while remote input may be from a remotely placed HMI or other control equipment. However, the controller also responds to the feedback loop that feeds information back to the controller. This feedback loop offers a process variable that is then compared to the setpoint to determine when the system should stop. This is why closed loop controllers are sometimes called feedback controllers.
In industrial control, control loops may be associated with the physical control of the motor shaft in relation to some other thing. So, for example, the position of a part, speed in reference to time, or the torque delivered by the motor.
What are the Advantages of a Closed-Loop System?
Closed-loop controllers are superior to open-loop controllers in several ways. Closed-loop systems can
- stabilize unstable processes
- improve reference tracking performance
- reduce sensitivity to parameter variations
- increase accuracy
- increase reliability and efficiency, especially in DC drives
Keep in mind closed-loop systems can be costlier, more complicated, and require more maintenance.
Are you looking for a great HMI or Operator Interface for your factory floor? AX Control sells a variety of Pro-face Xycom options, including the Proface GP3000 and Proface GP4000 series. Talk to our team today for your personalized RFQ!
You must be logged in to post a comment.