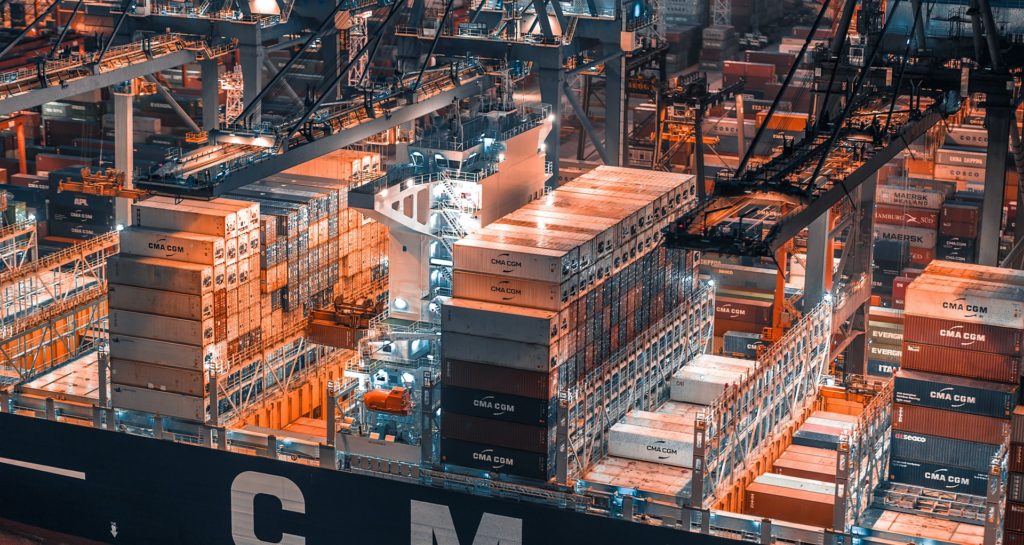
Just-in-time supply chains have been the standard for many companies for decades. Originally developed in the 1950s by Taiichi Ohno, a Toyota engineer, this inventory philosophy relies on suppliers delivering components just as they are needed. This reduces the need to tie up capital in on-hand inventory, as well as the cost for warehouse space to house it all.
Such lean manufacturing practices have been widely adopted across the world. Why? Because they work. But after months of supply chain woes caused by the pandemic, many are questioning whether just-in-time is right for their facilities.
Back to the Original J-I-T Concept
And yet, the Just-In-Time concept is not what’s flawed here. Instead, industries have strayed far away from the original “lean” concept. Now it’s time to return to J-I-T roots.
Back in the 1950s when Toyota, and then Honda, began using just-in-time delivery, they used suppliers close to their manufacturing facilities, sometimes within a five-mile radius. Deliveries occurred several times a day, ensuring parts arrived when needed.
But global supply chains don’t allow for this sort of fast response, even in good times. It takes an average of 15 to 30 days for cargo ships to cross the Pacific Ocean. Ships too large to enter the Panama Canal must commit to docking in only a few West Coast ports. In today’s current climate, docking wait times can extend for up to a week.
Add to this the ongoing driver shortage. Offloaded cargo waits at port for days until a truck driver becomes available. Then the next part of parts delivery begins. For East Coast manufacturers, that means waiting for trucks to cross the continent.
Today’s long and fragile supply lines mean once-a-month deliveries are more likely than early-concept multiple times a day. And yet, it’s not feasible for most manufacturers to only source from a 5- or even 100-mile radius like Toyota.
The Advantages of Nearshoring Supply Chains
Even if you can’t bring supply chains that close, reshoring has many benefits. Costs reduce. Resilience increases. Most importantly, response times drop. This allows you the confidence in knowing parts will arrive when you need them, or within a day or two. It certainly limits or eliminates the month-or-longer lead times.
Recent supply chain issues aren’t going to just disappear overnight. Even if the pandemic ended tomorrow, problems would remain. More to the point, the problems of the last year should be a warning: it’s time to change business-as-usual for good. Those who look for ways to improve now will be ready for the next major event.
Looking to keep your legacy system alive? AX Control can help. We specialize in hard-to-find components for legacy Pro-face, GE, Woodward, Horner, and Fuji systems. Talk to our team today!
You must be logged in to post a comment.