For many jobs in the Industrial Automation industry, protective work shoes are a necessity. In some cases, personal protective equipment is a requirement to even access the factory floor. Healthy feet are crucial for ease of movement; Lt. Dan from Forrest Gump taught us that.
Even when PPE footwear isn’t required, it’s often still a good idea to protect your feet from damage by rolling or falling objects, to protect from sharp objects beneath your sole, or to protect from electric shock. In any situation where a possibility of injury exists, workers should adopt a “better safe than sorry” approach.
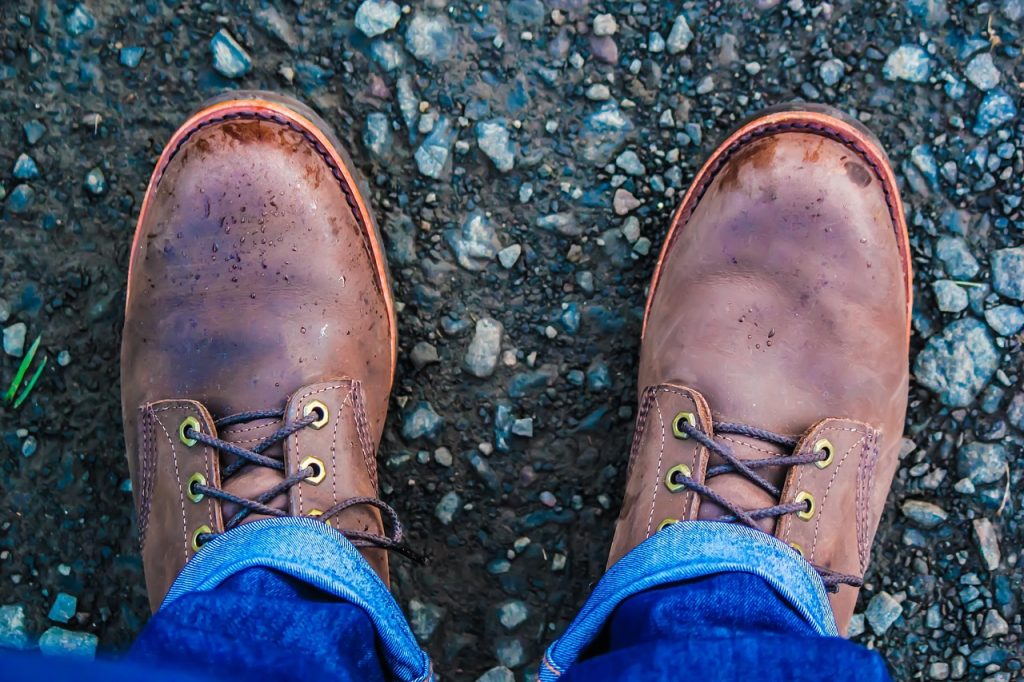
While OSHA (Occupational Safety and Health Administration) dictates how personal protective equipment is used, certification standards for safety shoes are actually provided by ASTM International.
How to read ASTM specifications
Footwear manufactured under these safety specifications must be marked somewhere on at least one shoe, typically on the surface of the shaft, gusset, tongue, or quarter lining. A rectangular border surrounds this marking, which typically has a 4-line format. Line one includes the ASTM code, for example, ASTM F2413-18. Line two identifies whether the shoe is made for men (M) or women (F) and notates if it offers impact resistance (I) or compression resistance(C.) Lines three and four identifies protection from other hazards. This includes (EH) for electrical hazard protection, (SD) for excess static electricity, (PR) for puncture resistance, and (Mt) for metatarsal protection.
ASTM f2413-18 vs ASTM f2413-11
Three of the most common codes you’re likely to come across will be ASTM F2413-05, ASTM F2413-11, and F2413-18. The first of these codes (F2413-05) was the 2005 Standard Specification for Performance Requirements for Protective (Safety) Toe Cap Footwear. It was reviewed and updated in 2011 and replaced with F2413-11. Another update was published in 2018. If you notice, it’s the same code except for the last two digits after the dash, which represents the year of publication. The 2018 update made changes to how shoes were tested, rated, and how these ratings were listed on labels.
Safety options for work shoes include
Steel Toe or Alloy Toe Work Shoes
These shoes have toe reinforcement to protect the front of the foot from falling objects. Alloy toe shoes use lighter-weight materials like titanium or aluminum.
Slip-resistant Work Shoes
Slip-resistant work shoes have rubberized or patterned soles. This helps workers maintain traction on wet, oily, or slippery surfaces.
Electrical Hazard Protection
EH-rated footwear will reduce the likelihood of electrocution by impeding the flow of electricity through the shoe into the ground. EH-rated footwear only offers the rated protection in dry settings. Also, EH-rated footwear is not retested after the fact. That means it’s not tested once it’s in use to ensure factory standards are still met. Although EH-rated footwear offers protection, it’s considered a secondary measure.
Safety shoes come in a variety of styles. For heavy industrial settings, boots are likely the first choice. But in light industrial or for staff who primarily works in lab settings, there are also safety sneakers, booties, and clogs.
Things to consider before buying work shoes
Safety shoes are an investment. So don’t be in a rush when you’re considering which pair you’re going to buy. Make sure shoes fit properly since most safety shoes won’t stretch like sneakers or thin, leather boots designed for casual wear. Make sure to buy a pair that meets all the safety requirements of your job.
Also, consider your job. If your work takes you through brush or muck, you may need a taller boot. If you’re always indoors, consider shorter to keep the weight down.
Finally, make sure your safety shoes are comfortable. There’s nothing so annoying as wearing uncomfortable shoes for eight hours a day. Don’t forsake comfort to save a few dollars.
Top Tips for Improving Safety Shoe Comfort
Here are a few tips for improving your on-the-job comfort.
- Try to shop for work shoes after work or in the afternoon after you’ve been on your feet for several hours. Your feet naturally swell during the day. This helps ensure you purchase the correct size for hours eight, nine, or ten, not just hour one.
- Wear the right socks. Wool or wool-blend socks are naturally wicking and will keep your feet dry, comfortable, and smelling rosy (well…maybe we’ll stick with dry and comfortable.) Cotton or polyester socks tend to trap moisture. However, that’s bad for your feet and your boots.
- Keep your boots dry and clean. Not only will moisture and muck decrease the lifespan of your expensive footwear, but it can also affect how they wear. Stiff leather can chafe, and dried mud can infiltrate and bother your skin. Brush your boots with a stiff brush to remove mud. Let them air dry if they’re wet, or fill with newspaper if they’re soaked to speed up drying.
- Rotate pairs. If you can afford two pairs of work shoes, you’ll end up getting more use out of both. The downtime allows each pair to fully dry out between uses. Plus your feet will be more comfortable.
Summing it up
Look at it this way: an extra $100 spent now breaks down to less than a nickel an hour difference over the next work year(2080 hrs x .05=104.) You don’t want to be the guy standing there with sore feet this time next year thinking “Boy, if I had a nickel for every time I wished I had spent the money on more comfortable work boots….oh wait, I kinda do.”
Want to know more about safety? Read our blog about Common OSHA violations and how to avoid them.
The information contained in this article is intended for general information purposes only and is based on information available as of the initial date of publication. No representation is made that the information or references are complete or remain current. This article is not a substitute for review of current applicable government regulations, industry standards, or other standards specific to your business and/or activities and should not be construed as legal advice or opinion. Readers with specific questions should refer to the applicable standards or consult with an attorney.
You must be logged in to post a comment.