Technological advancements are wonderful things, but they also come with their fair share of hurdles. One of the most significant things people in automation must overcome is obsolescence—with quickly changing processes, you never know when something will go the way of the dodo. Read on to learn how to manage obsolescence in industrial automation.
What Is Industrial Automation?
Previous industrial revolutions brought the world machinery that could do tougher jobs than humans could handle. The newest industrial revolution gives humans the ability to hand off the work of operating those machines to autonomous systems, including artificial intelligence.
As with any revolutionary event, there are many people who shy away from the changes. Some believe that industrial automation will hurt the job market, but that does not necessarily need to be the case. If a company is committed to keeping on their staff, the costs they save on the factory floor can go right back into their workers, training employees who once operated machines to do other tasks.
It’s important to remember that automation is not a purely positive process. Despite increasing productivity, automated systems come with high price tags and potentially a reduction of ethical human oversight.
Defining Obsolescence
The literal definition of obsolescence is “the act of becoming no longer produced or used; out of data.” In industrial marketing, obsolescence can refer to a few different functions, from parts that cease production to resources that become impossible to obtain.
Most of the time, obsolescence comes from the original equipment manufacturer (OEM)—when they stop producing a given part, the main source of acquisition is cut off. They may be upgrading to a new version of the part, or they may be going out of business themselves.
Types of Obsolescence
When talking about industrial automation, you need to understand the various types of obsolescence you may encounter.
- Aesthetic obsolescence. This occurs when the look or style of equipment phases out. While style isn’t everything, it can impact the equipment and parts available to you for replacements. For instance, a machine’s shell from the 1970s will be incredibly difficult to replace.
- Economic obsolescence. You’ll see economic obsolescence when there are more affordable alternatives to produce. No manufacturer wants to spend money making something less efficient, so when new ways to produce are discovered, you can expect older products to become obsolete.
- Functional obsolescence. This happens when an item has outdated design features that are difficult to update. For instance, in a world of touchscreen smartphones, Blackberry’s keypad fell off the face of the planet.
- Legal obsolescence. Laws are constantly changing and evolving, which can impact what parts can and cannot be produced. When shifting legal waters prohibit production, parts can cease production due to legal obsolescence.
- Technological obsolescence. Just as laws are ever in motion, so too is technology. When major shifts and advancements happen, you can expect to see older products phased out in favor of updated tech.
What Obsolescence Can Do To Your Facility
Most of the time, it’s possible to move forward with obsolescence—parts, resources, and services that are obsolete are usually still accessible, but for a higher price. However, that “higher price” may be much higher in some cases.
You need to consider that it isn’t only a hard-to-find part that’s needed to fix an obsolete machine; you will also need to find someone who is knowledgeable about a piece of technology that is no longer in circulation.
However, there are often replacements available that come from parts still in production. Most of the time, when something is discontinued, it is replaced with a similar, slightly improved product. Depending on what you need to fix your machine, the updated product may have a very similar part that you can retrofit as a substitute for the exact part that’s broken.
Every once in a while, though, an exact substitute is the only thing that will do the trick. That’s why it’s important to have a plan for what your company will do about obsolescence.
Set Up a Diverse Strategy
With any given industrial automation facility, you have tons of different pieces of equipment that will all require repair from time to time. In order to effectively manage all these moving parts, you’ll need a diverse strategy that addresses multiple factors.
Set up a team that keeps track of all your equipment and the condition that your machines are in. This will help you understand what is needed before things begin to break down.
Risk Assessment Tactics
When you’re building your plan, be sure to take risk management into account. You should prioritize the systems most vital to your business—if a machine goes down, how much will it impact your productivity? You shouldn’t fully disregard systems that won’t affect you as much, but you can put them lower on the priority list.
Have an Emergency Plan
Even with a team of people trying to keep an eye on all your equipment, emergencies willhappen. When they do, it’s better to have an emergency plan to get you back up and running than to experience indefinite downtime.
Whether you hire out for repairs or you have an internal team, make sure to have a quick response protocol so you can get eyes on the problem as soon as possible.
Organize Everything
Many facilities have excess parts and manuals for when things go wrong. The best thing you can do to set yourself up for success when something breaks down is to keep all your parts and manuals well-organized.
Understand That Obsolescence Isn’t the End of the World
There are several companies you can team up with that sell industrial automation parts in a variety of conditions, like AX Control. While we do sell new parts, we also have a selection of surplus and reconditioned industrial automation parts, which means you don’t need to worry as much about obsolescence! If there’s an older part you need, there’s a good chance we have it.
Now that you know how to manage obsolescence in industrial automation, do what you can to set yourself up for success. Just remember that a little obsolescence here and there is something you can work with.
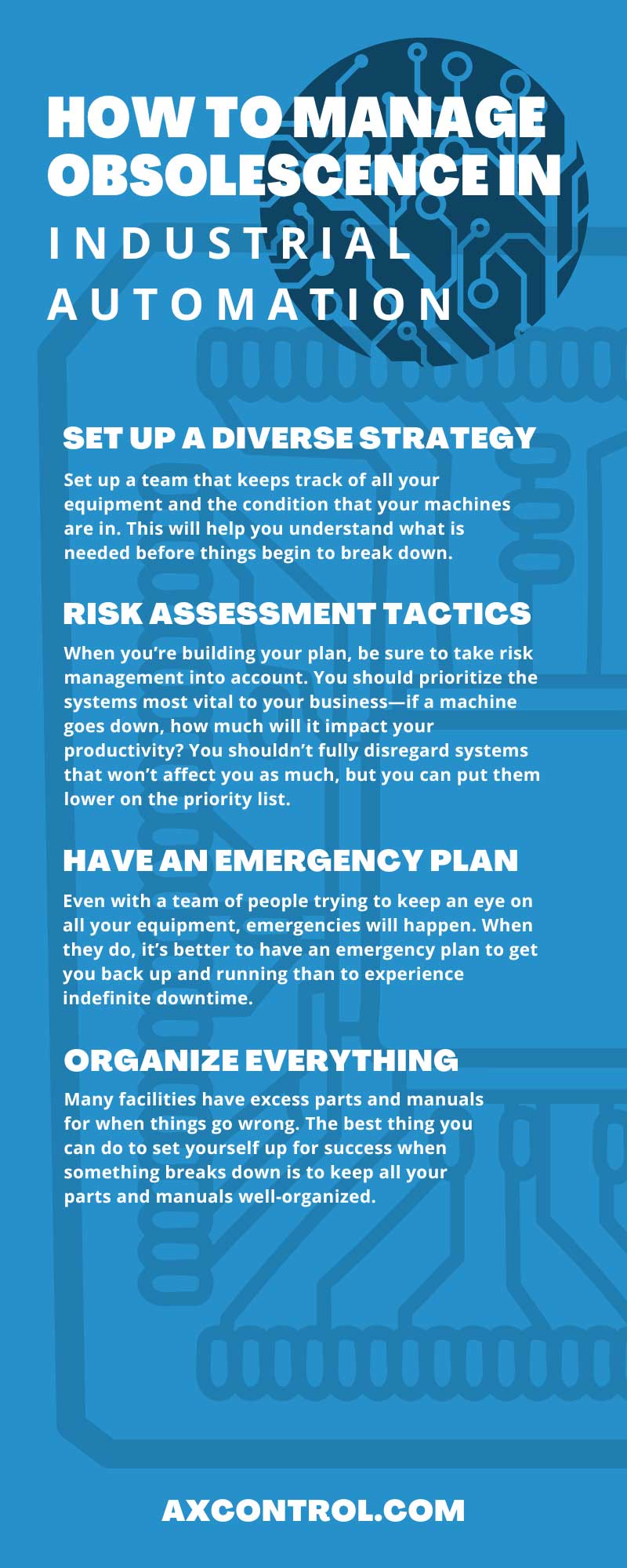
You must be logged in to post a comment.