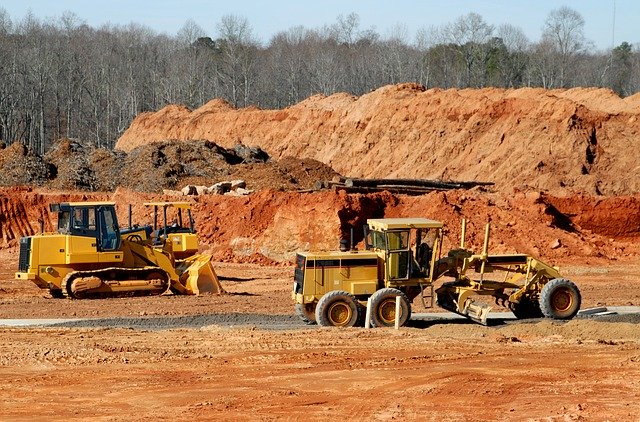
Disruptive technology, as a term, has been with us for over two decades. But disruptive technologies like automation have been with us for much longer. Disruptive technology is some new product or innovation that creates a new market or disrupts an established one. Henry Ford’s Model T was a disruptive technology that revolutionized transportation over 110 years ago.
Such innovations are found across markets. When video streaming service Netflix first came on the scene it disrupted cable and video rental brick and mortar chains. Now it’s disrupting Hollywood production models by creating its own content.
Other disruptive technology examples include cheap, portable transistor radios. These were completely different from the large, expensive vacuum-tube radios that preceded them. The Internet is another example. It killed off print encyclopedias like Brittanica and World Book while changing the world in countless ways. This shows how new technologies can change their associated industries by changing markets or by creating new ones.
In the last few decades, disruptive technologies within automation have made a significant impact on many industries. Here’s a list of some of the most important changes and the sectors affected by those changes.
Changes to the Automotive Industry
Car manufacturers were early adopters of industrial robotics. They now use robots for a wide variety of tasks including painting surfaces, welding, and assembly. Many plants use robots integrated with machine vision for inspection processes.
In the wake of the global pandemic, plants that relied on heavy automation saw significantly less impact on their outputs due to workforce stoppages than traditional factories. As countries like Germany use more robotics to offset labor shortages, this expansion in automation should continue.
Meanwhile, automated functions are slowly integrating into automobiles heading to consumers. Early automated functions like predictive emergency braking and cruise control are now standard in most cars. Top-of-the-line models now offer advanced features like lane departure warnings, blind-spot detection, and traffic jam assist. By 2025 many cars will offer fully automated safety options and highway autopilot features.
Automation in Healthcare
While much of the healthcare industry is impossible to automate due to the need for empathy and the power of human care, robotics and automation have still made a significant and impressive impact on the sector.
Medical automation may still include human guidance and interaction. For example, automated kiosks may offer patients their first instructions upon entering a doctor’s waiting room, automating steps like scanning new insurance cards, and updating patient information in the hospital database. But this is often followed by interaction with an on-site nurse or front office staff member who can then double-check this information. Additionally, such automated systems allow for healthcare staff to reduce wasted time by automating some aftercare interaction and can improve insights by providing better data insights to providers for performance improvement.
Automation has also spurred healthcare innovations like surgical robots for delicate surgeries like membrane removal for macular degeneration or laparoscopic surgical robots that help surgeons with keyhole procedures. Surgical robotics is expected to be a $20 billion industry by 2024.
In the wake of COVID-19 outbreaks, some hospitals added autonomous ultraviolet cleaning machines. These machines emit a strong UV light to slice apart the virus’s genetic material and can clean a room four times faster than human workers.
Older patients are also benefiting from automation. Automated pill dispensers can dole out months’ worth of medicine on a regulated schedule, and can even alert an offsite caregiver if medicine hasn’t been taken from the dispensing cup on time. This new technology will allow older patients the opportunity to live independently for a longer time.
Automation in Construction
Productivity in construction barely changed in the sixty years between 1950 and 2010. Over that same time, manufacturing increased its output by a factor of eight and agriculture by a factor of sixteen. But in the last decade, construction has begun to adopt more automated technologies, and the result has been an annual output increase of roughly 3.8%, the fastest real output growth of any goods-producing sector.
The technologies that are driving this growth are as varied as the construction industry itself. Robots are now being used for bricklaying, and large automated machines are paving roads. Some are combining both things, laying down brick roadways like a woven carpet.
Automation is also helping control traffic flow around construction sites. This minimizes accidents and the impact on surrounding communities. Automation and data analytics may even be used to schedule some projects to further limit the impact on traffic.
Additive manufacturing (3D printing) is also being used in construction for the creation of facades and components. Some architects have used additive manufacturing to 3D print entire structures. This technology reduces the window for human error, offers the potential for zero-waste construction, and opens up the window to creativity and innovation.
Finally, construction is using automation to improve on-site efficiencies through building information modeling. This allows for the planning, design, and management of a project to come together in a unified plan that identifies issues before work begins, allowing for improved scheduling of labor and materials and the elimination of costly mistakes and delays.
You must be logged in to post a comment.